China Solenoid Valve customized with no MOQ
customized solenoid valve as request
We specialize in providing customized solenoid valves tailored to meet the specific challenges of your work environment. Whether you require high-pressure, low-pressure activation, or valves capable of operating in extreme high or low temperatures, we offer solutions built to your exact specifications. Our product range also includes Emergency Shut-off solenoid valves and manual control options for enhanced safety and control.
What sets us apart? We offer fully customized solutions with no MOQ, ensuring that we can meet the needs of any project, no matter the size. Our advanced production facility follows international standards, including ANSI, API, DIN, GOST, BS, JIS, and China GB, ensuring high-quality performance in even the most demanding conditions. At BYZER, we’re committed to delivering innovation, quality, and flexibility, all without compromise.
Cast iron Butterfly valve
PVC Butterfly valve
High Temperature Butterfly valve
REQUEST A QUOTE FOR MORE DETAILS
How to buy a right Solenoid Valves for your project
What is Solenoid Valve?
Solenoid valve is an electromechanically operated valve, primarily used to control the flow of liquid or gas in a system. The valve is operated by an electric current running through a solenoid (a coil of wire), which either opens or closes the valve. Solenoid valves offer precision control and are widely used in automation systems due to their ability to switch quickly and operate remotely.
How Does Solenoid Valve Work?
solenoid valve is an electrically controlled valve that uses a solenoid (an electromagnetic coil) to regulate the flow of liquids or gases in a system. The basic working principle of a solenoid valve involves converting electrical energy into mechanical motion, allowing the valve to open or close automatically based on signals from a control system.
Here’s a step-by-step breakdown of how a solenoid valve works:
1. Resting State (Normally Open or Normally Closed)
Solenoid valves come in two primary states:
- Normally Closed (NC): In this state, the valve remains closed when no power is applied, blocking the flow of fluid.
- Normally Open (NO): In this state, the valve remains open when no power is applied, allowing fluid to pass through.
When the valve is in its resting state, the plunger is either sealing the valve (NC) or staying out of the flow path (NO).
2. Electric Signal Applied
When an electrical current is passed through the solenoid coil, it generates a magnetic field. This magnetic field creates a force that moves the plunger inside the valve. The direction of movement depends on whether the valve is normally open or normally closed.
- In a Normally Closed (NC) valve, the magnetic force pulls the plunger up, lifting it away from the valve seat, allowing the fluid or gas to flow through.
- In a Normally Open (NO) valve, the magnetic force pulls the plunger down, closing the valve and stopping the flow.
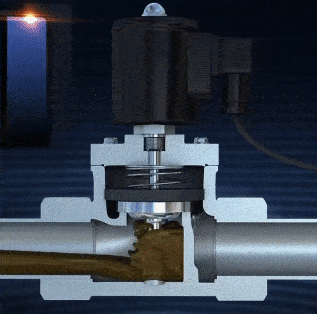
3. Controlling Flow
The valve opens or closes based on the presence or absence of the electrical signal, which controls the flow of liquid or gas through the valve. In more complex systems, solenoid valves can also be used for regulating flow direction or mixing fluids.
4. Return to Resting State
When the electrical current is cut off, the magnetic field disappears. In response, a spring inside the solenoid valve pushes the plunger back to its original position. This restores the valve to its default state—either closing (NC) or opening (NO) the flow path.
What Are Solenoid Valves Used For?
Solenoid valves are highly versatile components used in a wide range of applications where precise control over the flow of liquids or gases is required. Their ability to operate quickly, reliably, and remotely makes them essential in various industries. Here’s an overview of the common uses of solenoid valves:
1. Fluid and Gas Control in Industrial Automation
In industrial systems, solenoid valves are widely used to regulate the flow of fluids and gases. They provide fast, precise control in automated machinery and equipment, such as:
- Pneumatic and hydraulic systems
- Compressed air control in manufacturing processes
- Chemical dosing systems in factories
2. Water Treatment and Irrigation Systems
Solenoid valves play a crucial role in controlling water flow in large-scale treatment plants and irrigation systems. They are used to automate the process, ensuring efficient distribution of water and preventing wastage. Applications include:
- Water purification systems
- Automatic irrigation systems
- Wastewater treatment plants
3. HVAC Systems
Heating, ventilation, and air conditioning (HVAC) systems rely on solenoid valves for the precise control of air and fluid flow. They are essential for maintaining proper temperatures and optimizing energy use in:
- Refrigeration systems
- Air conditioning units
- Boiler systems
4. Medical and Laboratory Equipment
In the medical and pharmaceutical industries, solenoid valves are used to manage the flow of gases and fluids in critical environments. Their reliability and precision are vital for:
- Oxygen control in ventilators
- Fluid control in dialysis machines
- Laboratory instruments for fluid sampling

5. Automotive and Transportation Systems
Solenoid valves are used in automotive systems for controlling various functions, such as fuel and emission management. Common applications include:
- Fuel injection systems
- Emission control systems
- Transmission fluid regulation
6. Oil and Gas Industry
In the oil and gas sector, solenoid valves help control the flow of hydrocarbons and gases in pipelines, ensuring safety and operational efficiency. They are critical in:
- Wellhead control
- Pipeline shutdown systems
- Gas distribution networks
7. Food and Beverage Processing
The food and beverage industry uses solenoid valves to ensure hygienic control over the flow of ingredients, cleaning agents, and other fluids. They are essential for:
- Beverage dispensing systems
- CIP (Clean-in-Place) processes
- Food processing lines
8. Fire Safety Systems
Solenoid valves are a key component in fire suppression and sprinkler systems. They help control the release of water, foam, or gas in the event of a fire, ensuring rapid response and safety in:
- Fire suppression systems
- Foam dispensing units
- Gas shut-off systems
Advantages of Solenoid Valves
1. Fast and Precise Operation
One of the biggest benefits of solenoid valves is their rapid response time. Solenoid valves open and close almost instantly when an electric signal is applied or removed. This precision control is essential in applications that require immediate actuation, such as emergency shut-off systems, automated processes, and fluid dosing.
Advantage: Quick actuation enhances control accuracy and reduces the response time in critical situations.
2. Remote Control and Automation
Solenoid valves can be easily integrated into automated systems, allowing for remote control. This makes them ideal for large, complex setups where manual intervention would be inefficient or dangerous. In industries like oil and gas, water treatment, and HVAC, solenoid valves are often part of larger automated networks that can be monitored and adjusted remotely.
Advantage: Improved flexibility and convenience for remote operation, especially in hazardous or hard-to-reach locations.
3. Compact and Space-Saving Design
Compared to other valve types, solenoid valves are typically more compact, making them suitable for installations where space is limited. Despite their small size, they can handle high-pressure and high-flow applications, making them versatile for different pipeline setups.
Advantage: Compact size allows for easy integration into tight spaces without compromising performance.

5. Low Maintenance
The design of solenoid valves is relatively simple, consisting of few moving parts. This leads to lower wear and tear, resulting in minimal maintenance requirements over the valve’s lifespan. In industries that rely on continuous operation, reduced downtime for maintenance is a significant advantage.
Advantage: Low maintenance costs and reduced downtime make solenoid valves a cost-effective choice for long-term use.
6. Compatibility with Extreme Conditions
Solenoid valves can be designed to operate in extreme conditions, whether it’s high-temperature, low-temperature, high-pressure, or corrosive environments. They are available in high-temperature versions that can handle up to 350°C, low-temperature versions for cryogenic applications, and emergency shut-off variants for critical safety systems.
Advantage: Ability to handle extreme environmental conditions makes solenoid valves reliable even in the harshest industrial settings.
Solenoid Valve Parts
A solenoid valve is composed of several key components, each playing a crucial role in its operation. Understanding these parts helps to ensure proper selection, maintenance, and troubleshooting of solenoid valves. Below is an overview of the main parts of a solenoid valve and their functions:
Coil in Solenoid Valves
The coil is a critical part of a solenoid valve, as it is responsible for converting electrical energy into the magnetic force required to actuate the valve. It consists of wire, typically copper or aluminum, wrapped tightly around a core. However, the coil housing or enclosure plays an equally important role in protecting the coil from environmental factors and ensuring safe, reliable operation.

1. Coil Winding
The coil is typically made of copper wire due to its excellent conductivity. The wire is wound into tight loops around a cylindrical core, which forms the heart of the electromagnet. When an electric current passes through the coil, it generates the magnetic field necessary to move the plunger and control the flow of the valve.
- Materials: Copper or aluminum wire (copper is preferred for its conductivity).
2. Coil Enclosure (Molded Housing)
The coil is encased in a protective housing, which is molded around the coil winding to protect it from external elements such as dust, moisture, chemicals, and temperature fluctuations. This enclosure is typically made from durable thermoplastic materials designed to withstand the environmental stresses of the application.
Common Material: PET (Polyethylene Terephthalate), typically in black, is one of the most frequently used materials for coil housing. PET offers excellent thermal stability, moisture resistance, and mechanical strength, making it ideal for use in industrial environments where the valve may be exposed to tough conditions.
Other Materials: Depending on the operating conditions, other materials such as Epoxy or Polyamide (Nylon) may be used for enhanced thermal resistance or additional mechanical durability. For applications requiring higher heat tolerance, special plastics or metal housings may be used.
3. Thermal Class
The coil’s insulation is designed to handle specific temperature ranges, referred to as thermal classes. These classes define the maximum operating temperature of the coil before its insulation material begins to degrade. Common thermal classes include:
- Class B: Handles temperatures up to 130°C.
- Class F: Handles temperatures up to 155°C.
- Class H: Handles temperatures up to 180°C.
Selecting the appropriate thermal class ensures the solenoid coil can operate efficiently under the required environmental conditions without overheating or losing insulation integrity.
4. Voltage and Power Ratings
The coil’s voltage rating is another crucial factor in its design. Coils can be designed for different voltage ranges, such as low-voltage DC systems (e.g., 12V or 24V) or higher-voltage AC systems (e.g., 110V or 230V). Matching the coil’s voltage rating to your system ensures proper performance and avoids potential damage to the solenoid valve.
5. Coil Connector
The coil connector or terminal is where the coil is wired to the control system, allowing electrical current to flow through the winding. Different connector types are used depending on the application:
- DIN Connectors: Standardized connectors that are common in industrial applications, allowing easy replacement or maintenance of the solenoid coil.
- Flying Leads: Wires coming directly from the coil for simpler, direct connections.
These connections are usually waterproof and designed to resist corrosion or damage in harsh environments.
Plunger and Core
In a solenoid valve, the plunger and core are two distinct yet closely interacting components that play a vital role in the valve’s operation. The plunger is the movable part that opens or closes the valve, while the core is stationary and provides magnetic guidance for the plunger. These two components are aligned when installed and function together to control the flow of fluid or gas.
1. Material
Both the plunger and core are typically made from magnetic stainless steel or ferromagnetic alloys that respond to the electromagnetic field generated by the solenoid coil. These materials are carefully selected to ensure optimal magnetic permeability, durability, and resistance to wear in demanding environments.
- Plunger: Often made from magnetic stainless steel, designed for movement within the solenoid valve.
- Core: Made from similar magnetic materials, but remains stationary, guiding the magnetic field and the plunger’s motion.
2. Interaction Between Plunger and Core
When the solenoid coil is energized, the magnetic field generated by the coil pulls the plunger toward the core. The core, being stationary, acts as the anchor point for the plunger’s movement, guiding it to create or break the seal that controls fluid or gas flow. The plunger and core must align perfectly for the valve to function smoothly.
- Movement: The plunger moves toward the core when the coil is energized, enabling valve operation.

3. Armature Extension for Thermal Isolation
In high-temperature and low-temperature solenoid valves, an armature extension or plunger extension is used to thermally isolate the solenoid coil from extreme temperatures. This extension sits between the coil and the valve body, protecting the coil from excessive heat in high-temperature applications or freezing conditions in low-temperature environments.
- High-Temperature Application: The extension helps prevent the transfer of heat to the solenoid coil, maintaining operational integrity.
- Low-Temperature Application: The extension prevents the coil from exposure to freezing temperatures, ensuring smooth operation in cryogenic conditions.
4. Thermal Management
The plunger and core are designed to operate efficiently even in extreme environments. In high- or low-temperature applications, the use of advanced materials and the armature extension ensures reliable valve operation. The thermal isolation provided by the extension reduces the risk of expansion or contraction due to temperature changes, preventing mechanical binding or wear.
- Thermal Expansion Control: The design allows the valve to accommodate expansion and contraction without affecting functionality.
5. Return Mechanism
A spring is typically integrated with the plunger to ensure it returns to its default position (open or closed) when the solenoid is de-energized. This spring is commonly made of stainless steel or other corrosion-resistant materials, ensuring smooth operation and a consistent response to electrical signals.
- Spring Material: Stainless steel or other corrosion-resistant materials.
Diaphragm
The diaphragm is a flexible membrane used primarily in pilot-operated solenoid valves to control fluid or gas flow. It operates by creating a seal between different pressure zones in the valve and moves based on pressure differentials to open or close the valve. The diaphragm is critical in enabling smooth valve operation with minimal mechanical force.
1. Material
The diaphragm needs to be both flexible and durable, so its material is selected based on the fluid or gas it will encounter and the operating conditions. Common materials include:
- EPDM (Ethylene Propylene Diene Monomer): Used in water and air applications, with excellent heat and ozone resistance.
- Nitrile (Buna-N): Often selected for oil and gas applications due to its strong resistance to petroleum-based fluids.
- Viton (FKM): Ideal for chemical environments, especially those involving aggressive fluids or higher temperatures.
- PTFE (Teflon): Known for its superior chemical resistance and ability to handle harsh environments.
The material choice ensures the diaphragm can withstand the operating pressures and fluids in the system without degrading.
2. Pressure and Temperature Tolerance
Diaphragms must handle wide temperature ranges and significant pressure differentials across the valve. Different materials offer varying resistance to temperature extremes and pressure conditions:
- High-Temperature Diaphragms: Materials like Viton and PTFE can handle elevated temperatures without breaking down.
- Low-Temperature Diaphragms: EPDM retains its flexibility at lower temperatures, making it ideal for colder environments.
- Pressure Resistance: Diaphragms are designed to handle the pressure differences on either side of the valve, ensuring effective operation under various pressures.
3. Durability
Given the repetitive movement involved in valve actuation, the diaphragm must resist wear and tear. It must also endure contact with corrosive or abrasive fluids, depending on the application. Over time, diaphragms may need to be inspected and replaced to maintain performance.
- Wear Resistance: High-quality diaphragm materials can withstand thousands of cycles, extending valve lifespan.
- Chemical Compatibility: Ensuring the right material is selected based on the chemicals or gases being controlled prevents premature wear or chemical degradation.

1. Material
The diaphragm needs to be both flexible and durable, so its material is selected based on the fluid or gas it will encounter and the operating conditions. Common materials include:
- EPDM (Ethylene Propylene Diene Monomer): Used in water and air applications, with excellent heat and ozone resistance.
- Nitrile (Buna-N): Often selected for oil and gas applications due to its strong resistance to petroleum-based fluids.
- Viton (FKM): Ideal for chemical environments, especially those involving aggressive fluids or higher temperatures.
- PTFE (Teflon): Known for its superior chemical resistance and ability to handle harsh environments.
The material choice ensures the diaphragm can withstand the operating pressures and fluids in the system without degrading.
2. Pressure and Temperature Tolerance
Diaphragms must handle wide temperature ranges and significant pressure differentials across the valve. Different materials offer varying resistance to temperature extremes and pressure conditions:
- High-Temperature Diaphragms: Materials like Viton and PTFE can handle elevated temperatures without breaking down.
- Low-Temperature Diaphragms: EPDM retains its flexibility at lower temperatures, making it ideal for colder environments.
- Pressure Resistance: Diaphragms are designed to handle the pressure differences on either side of the valve, ensuring effective operation under various pressures.
3. Durability
Given the repetitive movement involved in valve actuation, the diaphragm must resist wear and tear. It must also endure contact with corrosive or abrasive fluids, depending on the application. Over time, diaphragms may need to be inspected and replaced to maintain performance.
- Wear Resistance: High-quality diaphragm materials can withstand thousands of cycles, extending valve lifespan.
- Chemical Compatibility: Ensuring the right material is selected based on the chemicals or gases being controlled prevents premature wear or chemical degradation.
Valve Body
The valve body is the main structural component of a solenoid valve, housing all the internal components and forming the flow path for fluids or gases. It connects the inlet and outlet ports and serves as the foundation that holds components like the plunger, diaphragm, and O-rings in place. The valve body must be durable, corrosion-resistant, and compatible with the working fluid to ensure the system’s long-term performance.
1. Material
Valve bodies are made from a variety of materials, each selected based on the specific fluid or gas being handled, as well as the operating temperature and pressure conditions. Common materials include:
- Brass: A widely used material for general-purpose applications. Brass is corrosion-resistant and durable, making it ideal for water, air, and light oil systems.
- Stainless Steel: Known for its strength and high corrosion resistance, stainless steel valve bodies are used in harsh environments where chemicals, high temperatures, or aggressive fluids are present.
- Plastic (PVC, CPVC, PTFE): Used in chemical applications or water treatment systems where lightweight and chemical resistance are key. Plastic valve bodies are typically more cost-effective but can handle lower temperatures and pressures.
- Cast Iron or Ductile Iron: Employed in heavy-duty industrial applications where durability and resistance to mechanical stress are required, such as high-pressure steam or water systems.
Selecting the right material ensures that the valve body can withstand the rigors of the system without corrosion, leaks, or degradation over time.
2. Design and Construction
The valve body is designed to allow optimal fluid or gas flow while accommodating the valve’s internal components. The internal flow paths are engineered to minimize pressure drop and turbulence as the medium moves through the valve. Key design elements include:
- Inlet and Outlet Ports: Connect the valve to the pipeline, allowing fluid or gas to enter and exit. The ports must be compatible with the system’s piping, whether threaded, flanged, or welded.
- Flow Path: The valve body houses the flow path that directs fluid through the valve. This path is shaped to provide smooth flow when the valve is open and a tight seal when closed.
- Seating Surfaces: The valve body includes surfaces where the plunger, diaphragm, or ball seats to create a leak-tight seal when the valve is closed.
The design and construction of the valve body ensure smooth, efficient flow and reliable sealing in both open and closed states.
3. Temperature and Pressure Tolerance
The valve body must withstand the system’s operating conditions, including temperature extremes and pressure fluctuations. The material and thickness of the valve body are chosen to accommodate the maximum pressure and temperature ratings of the system:
- High-Pressure Tolerance: For high-pressure systems, valve bodies made from stainless steel or ductile iron are designed to resist deformation or cracking under intense pressure.
- Temperature Resistance: In high-temperature applications, materials like stainless steel or high-temperature plastics are chosen for their ability to maintain structural integrity. Valve bodies in low-temperature systems may also require specific materials to avoid brittleness.
Ensuring that the valve body is rated for the correct pressure and temperature conditions is critical for safe and reliable valve operation.
4. Corrosion Resistance
In applications where the valve body is exposed to corrosive fluids or gases, choosing a corrosion-resistant material is essential. For example, stainless steel and PTFE are highly resistant to chemical attacks, making them suitable for aggressive environments like chemical processing or wastewater treatment.
- Chemical Compatibility: The valve body material must be compatible with the fluid or gas it will contact to prevent corrosion or chemical reactions that could lead to leaks or failure.
- Coatings and Linings: In some cases, valve bodies may be coated or lined with materials like epoxy or PTFE to enhance their corrosion resistance without using more expensive base materials.
5. Connections
The valve body is designed to integrate seamlessly with the system’s piping and other components. Various connection types ensure compatibility with different installation methods:
- Threaded Connections: Often used in smaller systems or residential applications for easy installation and maintenance.
- Flanged Connections: Common in industrial systems, providing a secure, bolted connection that can handle higher pressures and flow rates.
- Welded Connections: Used in high-pressure or critical applications where leak-free operation is essential, as welding creates a permanent and strong joint.
Types of Solenoid valve
Butterfly valves are categorized based on various design features and functional aspects. Here’s a detailed explanation of the different types:
1. How many type of Solenoid valve
Solenoid valves come in various types, each designed to perform specific tasks and operate under different conditions. The choice of solenoid valve type depends on factors like the flow control requirements, fluid or gas being handled, and the operating environment. Below are the most common types of solenoid valves:
1. Direct-Acting Solenoid Valve
Overview: In a direct-acting solenoid valve, the plunger directly opens or closes the valve. This type does not rely on system pressure to assist in valve operation, making it ideal for low-pressure applications or situations where the valve must function without pressure assistance.
- Advantages: Simple design, quick response time, and the ability to operate without a minimum pressure requirement.
- Applications: Ideal for small flow rates, low-pressure systems, and tasks requiring immediate on/off control.


2. Pilot-Operated Solenoid Valve
Overview: A pilot-operated solenoid valve uses system pressure to help open or close the valve. The solenoid controls a small pilot valve that allows system pressure to act on a diaphragm or piston, which then opens or closes the main valve. This design allows for the control of larger flow rates with minimal power.
- Advantages: Handles higher flow rates and pressure with lower power consumption compared to direct-acting valves.
- Applications: Common in HVAC systems, water treatment plants, and other industrial systems requiring large volumes of fluid or gas control.
3. Proportional Solenoid Valve
Overview: A proportional solenoid valve allows for variable flow control, rather than the simple on/off operation of standard solenoid valves. The valve opens proportionally to the current applied to the solenoid coil, allowing precise control of the flow rate.
- Advantages: Enables accurate flow regulation and is ideal for systems requiring variable control rather than simple on/off.
- Applications: Commonly used in fuel injection systems, industrial automation, and flow metering applications.

4. Explosion-Proof Solenoid Valve
Overview: Designed for use in hazardous environments, explosion-proof solenoid valves are built to contain any internal explosions caused by sparks or heat generated by the solenoid coil. These valves are encased in heavy-duty housings that prevent flames or sparks from escaping into the surrounding atmosphere.
- Advantages: Provides safety in environments where flammable gases, vapors, or dust are present.
- Applications: Used in oil and gas, chemical processing, mining, and other hazardous environments.
5. High-Pressure Solenoid Valve
Overview: High-pressure solenoid valves are specifically designed to handle fluids or gases at very high pressures. These valves feature reinforced bodies, high-strength seals, and components to withstand extreme pressure conditions.
- Advantages: Capable of operating in high-pressure environments without leaks or failures.
- Applications: Suitable for hydraulic systems, high-pressure gas pipelines, and industrial processes requiring precise control under high pressure.
6. Cryogenic Solenoid Valve
Overview: Cryogenic solenoid valves are designed for ultra-low temperature applications, typically involving the handling of liquefied gases such as nitrogen, oxygen, or helium. These valves are constructed with materials that can withstand extremely low temperatures without losing functionality.
- Advantages: Performs reliably in extreme cold and resists freezing.
- Applications: Used in cryogenic systems, gas storage, and medical or industrial applications where low-temperature gases are handled.
2. Based on Connection Design
Threaded Connection
Overview: Threaded solenoid valves feature female threads on the valve body, designed to screw directly onto male-threaded pipes or fittings. This connection type is commonly used in smaller systems with lower pressure requirements.
Advantages:
- Easy Installation: No need for welding or special tools, making it quick and cost-effective to install.
- Versatility: Suitable for smaller bore sizes and low to moderate pressure applications.
- Flexibility: Allows for easy disassembly and reassembly, ideal for systems requiring frequent modifications.
Considerations:
- Leak Risk: Threaded connections can be more prone to leaks, especially in high-pressure applications or in systems with significant vibrations.
- Material Compatibility: Threads can wear over time and are best suited for non-corrosive environments, as corrosive fluids may damage the threads and lead to leakage.
Standards:
- BSP (British Standard Pipe): Widely used in Europe, Australia, and Asia, BSP threads include BSPT (tapered) and BSPP (parallel) variants.
- NPT (National Pipe Thread): Commonly used in North America, NPT threads feature a tapered design to form a tighter seal under pressure.
- G Thread (Metric BSPP): Known as G-thread in metric systems, this is a parallel pipe thread standardized under ISO 228, commonly used in Europe.
- GOST (Russian State Standard): Russia and former Soviet countries use GOST standards for threaded connections, with GOST 6357 being the primary standard for threaded fittings.
Applications: Ideal for residential plumbing, irrigation systems, and small-scale industrial setups, especially where ease of installation and maintenance is important.
Flanged Connection
Overview: Flanged solenoid valves feature flanges on the valve body that bolt to matching flanges on pipes. This connection design ensures a strong, leak-resistant connection, commonly used in larger systems with high-pressure or high-flow applications.
Advantages:
- Secure Connection: Flanged joints offer a robust, leak-resistant connection suitable for high-pressure systems.
- Maintenance-Friendly: Easy to remove for maintenance without disturbing the entire piping system.
- Durability: Well-suited for high-pressure, high-temperature applications, offering a stable and long-lasting connection.
Considerations:
- Space and Weight: Flanged connections tend to be bulkier, requiring more space and support during installation.
- Cost: Flanged connections typically involve higher material and installation costs due to their larger size and complexity.
Standards:
- ANSI (American National Standards Institute): Widely used in North America for flanged connections, including ANSI B16.5 for pipe flanges and flanged fittings.
- DIN (Deutsches Institut für Normung): The German standard for flanges, commonly used in Europe, such as DIN 2633 for steel flanges.
- JIS (Japanese Industrial Standards): Used in Japan and neighboring regions, JIS B2220 is a standard for flanged connections in industrial applications.
- GOST (Russian State Standard): Russia and other CIS countries use GOST standards for flanges, such as GOST 12820-80, a widely used flange standard in pipelines and industrial systems.
Applications: Ideal for heavy-duty industries like oil and gas, petrochemical, chemical processing, and water treatment plants, where high-pressure and high-temperature conditions require robust, leak-proof connections.
Welded Connection
Overview: Welded solenoid valves are permanently welded into pipelines, offering a highly durable, leak-proof connection. Welded joints are ideal for systems that operate under high pressure, high temperature, or where long-term reliability is paramount.
Advantages:
- Leak-Free: Welded joints eliminate potential leak points, making them ideal for critical applications.
- High Durability: Perfect for systems where reliability and safety are paramount due to continuous high-pressure operation.
- Maintenance-Free: Once installed, welded valves require minimal maintenance, as the permanent bond reduces the need for regular inspections.
Considerations:
- Permanent Installation: Welded connections are not easily removed, which can complicate maintenance or replacements.
- Skill Requirement: Welding must be done by skilled professionals to ensure a proper seal and alignment.z
Standards:
- ASME B16.25: A key standard for butt-weld fittings in high-pressure applications.
- ISO 1127: Specifies dimensions and tolerances for welded piping systems.
- GOST (Russian State Standard): GOST 16037-80 defines welded joints for industrial pipelines used in Russia and CIS countries.
Applications: Common in chemical plants, high-pressure pipelines, oil and gas industries, and power generation, especially where seamless, long-term connections are necessary.
Clamp (Quick-Connect) Connection
Overview: Clamp or quick-connect solenoid valves use clamps to secure the valve to pipes or tubing. This design enables easy and fast installation or removal, commonly used in sanitary industries that require frequent cleaning and maintenance.
Advantages:
- Quick Installation: No threading or welding required, making the installation process fast and easy.
- Hygienic: Excellent for sanitary applications, as they allow for easy disassembly and cleaning.
- Flexible: Perfect for applications where frequent maintenance is required.
Considerations:
- Pressure Limitations: Clamp connections are typically not suited for high-pressure systems.
- Connection Security: Clamps must be properly tightened to prevent leaks or detachment.
Standards:
- ISO 2852: International standard for hygienic clamp fittings, widely used in the pharmaceutical and food industries.
- DIN 32676: European standard for clamp connections, specifically used for sanitary applications in the food, beverage, and pharmaceutical industries.
Applications: Ideal for sanitary industries, including food and beverage processing, pharmaceuticals, and biotech applications where hygiene and ease of maintenance are critical.
Socket Weld Connection
Overview: Socket-weld solenoid valves are welded to pipes using a socket-welding process, where the pipe is inserted into a socket on the valve body and then welded. This method is used for high-pressure or high-temperature applications that require a strong and leak-free connection.
Advantages:
- Vibration Resistance: Socket welds provide a durable connection resistant to vibrations and mechanical stress.
- Leak-Tight: Provides a secure, leak-proof connection suitable for high-pressure environments.
- Compact: The socket weld design allows for a compact installation.
Considerations:
- Permanent Installation: Socket-welded valves are not easily removed for maintenance or replacement.
- Installation Skill: Precise welding by skilled professionals is required to ensure a proper seal and alignment.
Standards:
- ASME B16.11: Standard for socket-weld fittings, specifying dimensions and tolerances for high-pressure systems.
- ISO 1127: International standard for socket weld fittings, ensuring compatibility in industrial systems.
- GOST (Russian State Standard): GOST 30732-2006 outlines socket weld connections for high-pressure pipelines in Russia and CIS countries.
Applications: Commonly found in petrochemical plants, refineries, and high-pressure industrial systems where vibration and mechanical stress are factors.
Butt-Weld Connection
Overview: Butt-weld solenoid valves are welded to the pipe ends using a butt-weld process, creating a seamless and strong connection. This type of connection is commonly used in high-pressure and high-flow systems to reduce turbulence and ensure minimal pressure drop.
Advantages:
- Smooth Flow Path: The seamless design minimizes turbulence and pressure drop, ensuring efficient fluid flow.
- Leak-Free: Welded joints eliminate the risk of leaks, making them ideal for high-pressure and high-temperature systems.
- Durability: Butt-weld connections are long-lasting and highly durable, perfect for demanding industrial environments.
Considerations:
- Permanent Installation: Requires cutting for valve replacement or maintenance, making it less flexible than other connection types.
- Precision Installation: Skilled welding and precise alignment are necessary to ensure a secure, leak-proof seal.
Standards:
- ASME B16.25: Standard for butt-weld fittings in industrial applications, ensuring leak-proof and durable connections.
- ISO 1127: Specifies dimensions and tolerances for butt-weld fittings in industrial piping systems.
- GOST (Russian State Standard): GOST 16037-80 specifies butt-weld joints for industrial pipelines in Russia and CIS countries.
Applications: Used in high-flow, high-pressure systems in industries such as oil and gas, chemical processing, and power generation where reliability and smooth flow are essential.
Solenoid Valve Installation Guidelines
Proper installation of a solenoid valve is essential for ensuring optimal performance, reliability, and longevity. Follow these guidelines to avoid common issues and maintain the valve’s functionality over time.
1. Pre-Installation Cleaning
Before installing the solenoid valve, thoroughly clean and flush the piping system to remove any debris, dirt, or contaminants. Foreign particles can obstruct the valve opening or damage the sealing surfaces, leading to malfunction. For systems prone to debris or dust, it is recommended to install a filter or strainer upstream of the valve (filter mesh ≥ 80 mesh per cm²) to protect the valve.
2. Flow Direction and Coil Position
Ensure that the flow direction indicated by the arrow on the valve body matches the actual flow direction of the fluid in the pipeline. The valve coil should be installed upright and vertical to maintain proper function. Installing the coil horizontally or upside down can impair the valve’s operation and lifespan.
3. Check System Parameters
Before installation, verify that the pressure, temperature, and voltage specifications of the system match the parameters listed on the solenoid valve’s nameplate. Installing a valve with incorrect specifications can lead to performance issues or damage.
4. Media Cleanliness and Regular Maintenance
Ensure that the medium (fluid or gas) is clean and free of contaminants. Periodically clean the internal components of the solenoid valve during use to prevent buildup or blockages. When disassembling the valve for maintenance, inspect the seals and gaskets for wear or damage. Replace any worn or damaged parts immediately to maintain optimal sealing and prevent leaks.
5. Proper Installation Technique
When installing the valve, use a wrench to hold the valve body securely while tightening the pipe fittings. Avoid applying force directly to the solenoid coil or electrical connections, as this could cause internal bending, deformation, or loosening of the connections, potentially leading to leaks or malfunctions.
6. Operational Testing
After installation, test the solenoid valve by allowing fluid to pass through and actuating the valve multiple times. This ensures that the valve is functioning correctly before the system is fully operational. Only after confirming normal operation should the system be put into continuous use.
7. Electrical Wiring
Ensure that the solenoid valve is wired correctly according to the wiring diagram provided by the manufacturer. Incorrect wiring can lead to operational failures or damage to the valve. Follow electrical safety standards and use proper grounding to prevent electrical hazards.
8. Pressure Monitoring
Install pressure gauges both upstream and downstream of the solenoid valve to monitor pipeline pressure. This allows for easy observation of system conditions and ensures that the valve operates within the correct pressure range.
9. Pressure Differential
For proper operation, the inlet pressure must always be higher than the outlet pressure. If the outlet pressure exceeds the inlet pressure, the solenoid valve may remain in the open position, leading to a malfunction. Make sure the system maintains the correct pressure differential for reliable valve performance.
Let's Started Today!
If you’re seeking the ideal valve solution for your industrial projects, we’re here to support you.
Tell us your requirements, and our team will provide the guidance and information you need to make the best decision for your operations.
Reach out now to enhance your systems with our reliable and efficient valve technologies.
Support
info@byzervalve.com
Ask For Quote Now!
Reply Within 24 Hours
Your email is confidential and safe with us. Our team guarantees your privacy.