Industrial valve with actuator
Looking for Automatic Industrial Valves for Projects?
We are one of the leading producers of industrial valves at BYZER manufactures industrial grade ball valve, butterfly valve etc., with high quality. Each valve is manufactured in accordance with the most stringent international standards. Our advanced production facility China, enforced with ANSI, API,DIN,GOST, BS,JIS and China GB standards “By staying true to the principles of quality, innovation and a rebellious spirit, we’ll make certain that our products provide always the best quality paired with top performance.
Ball valve
Butterfly valve
Control Valve
Solenoid valve
angle seat valve
sanitary valve&fitting
check valve
flow indicator
REQUEST A QUOTE FOR MORE DETAILS
The Ultimate Guide: Buyers' Guide of Automatic Valve and valve Actuator
Chapter 1: How many Valve Actuator/Automation Types?
What is Manual valve
Valves are devices to control the flow of liquids and gases manually. They typically function by means of handwheels, levers, and gears, facilitating a simple and cost-effective mode of operation. These valves are commonly used in many applications because these are easy.
On the other hand, manual valves have some disadvantages. For example, big valves can be hard to manually open as they take a whole lot of work. Also, if one of the valves is in a dangerous or remote area, you may have to send someone out there on foot. The speed of operation is another issue. In the case of an emergency, for instance, manual valves might not be closed quickly enough. However, despite their difficulties and downsides, manual valves are relished for how dependable and simple to operate these devices are.

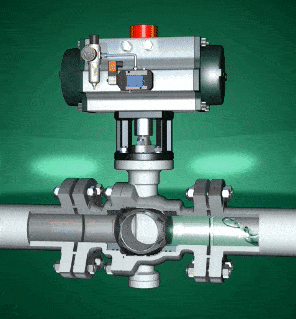
What is Pneumatic valve
In an industrial environment, pneumatic valves play a vital role in rapidly and efficiently controlling equipment by utilizing compressed air. These are especially great workout tools known for their quick two-position cut-offs and flow adjustments, making them quite versatile. These valves are quite handy in flammable or explosive areas, as they maneuver gases, liquids, oils, and even corrosive media safely. It is important to highlight that with the main valve, pneumatic accessories like actuators, positioners, solenoids, and limit switches also guarantee adaptability in different desired configurations.
Butterfly valves are also used in chemical processing, oil & gas, water treatment, and pharmaceutical sectors due to the non-sparkable option they provide. It is an important safety feature essential in areas that are unsafe and need work to be carried out effectively as well as safely. For the diverse and dynamic needs of operations, pneumatic valves serve as the heart of modern industrial automation, providing speed, reliability, and standardization.
What is Electric/Motorized valve
Electric/motorized valves use electric motors to regulate the functions. They help in controlling the flow very precisely. An ideal solution for any application, these grippers are suitable wherever shorter strokes and a higher level of automation are needed: perfect when it comes to tasks with more fine adjustments and remote monitoring. Made to handle water, gas, oil as well as chemicals while being able to withstand tough environments.
You can find them in HVAC systems, water treatment plants, oil and gas pipelines, and any manufacturing facility you could think of. This has made them indispensable in terms of reliability and energy efficiency, while also minimizing human error. Electric valves offer a wide range of customizable options with different actuators and feedback systems, which can be designed to meet custom requirements that provide precise control in an industrial process.
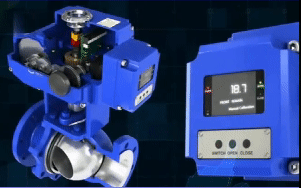
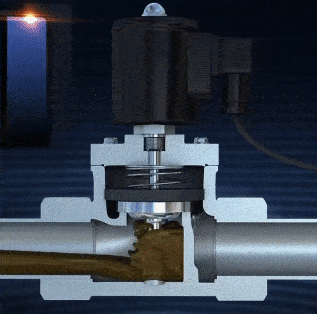
What is Solenoid valve
Solenoid valves are crucial for managing the flow of liquids or gases by utilizing an electric current. When this current creates a magnetic field, it moves a plunger to open or close the valve, providing quick and precise control. These valves excel in fast fluid management, making them essential in various industries such as water treatment, HVAC, automotive, and industrial automation.
Solenoid valves are versatile, capable of handling different media like water, air, oil, and gases. They come in multiple sizes and configurations to meet diverse requirements. By being part of automated systems, solenoid valves improve safety and efficiency, reducing the need for manual operations and ensuring consistent performance. Their adaptability and dependability make them a key component in modern industrial setups, guaranteeing smooth and efficient fluid control.
Chapter 2: How many Valve bodys(General Type) for Actuator
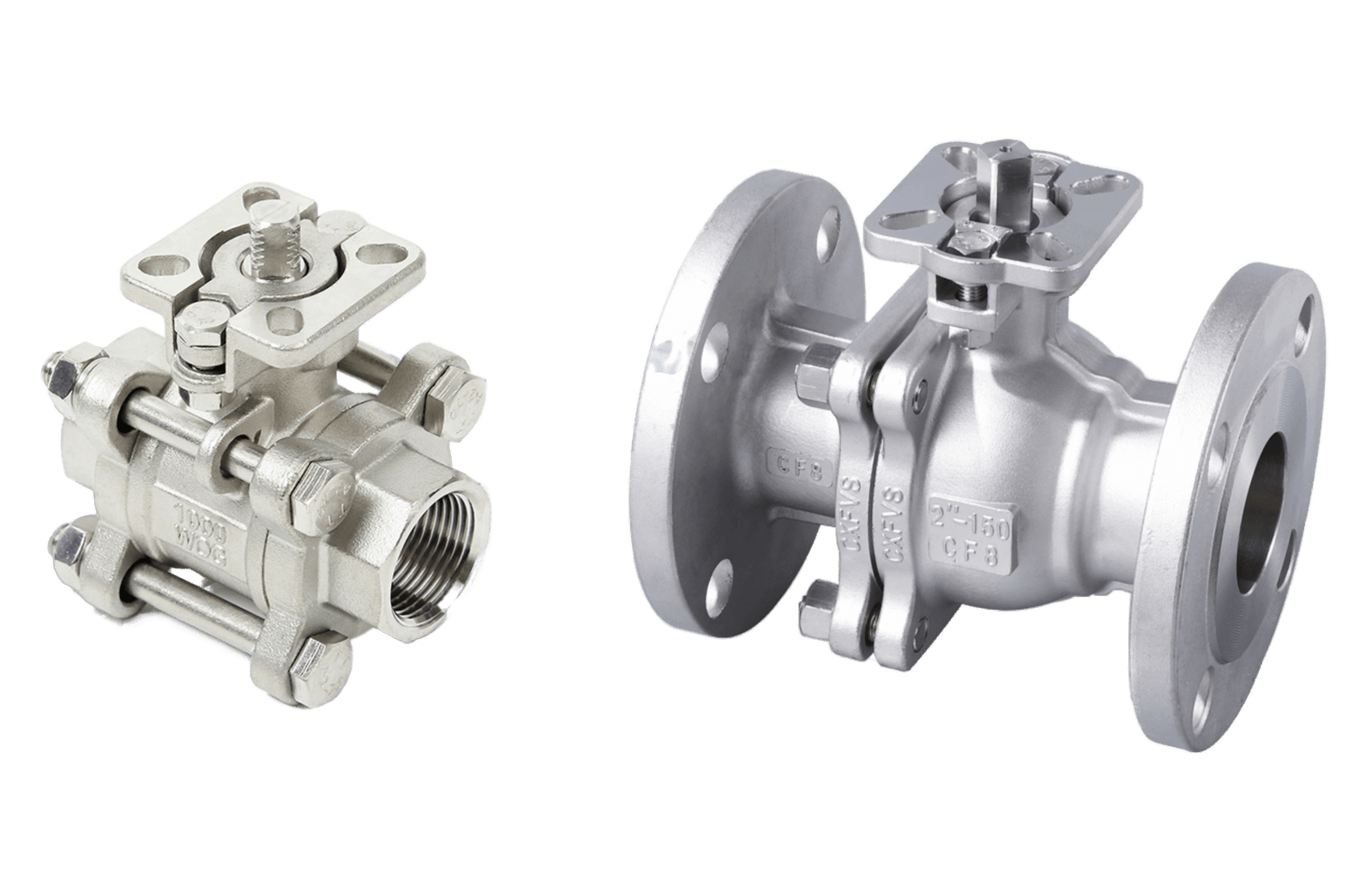
Ball Valve Bodies
Ball valves use a spherical disc with a hole through it, which aligns with the flow when open and blocks it when closed. They offer quick shutoff and low flow resistance when fully open.
- Advantages: Fast operation and tight sealing.
- Disadvantages: Poor throttling capabilities.
- Applications: Common in oil and gas, chemical, and water systems where rapid shutoff is essential.
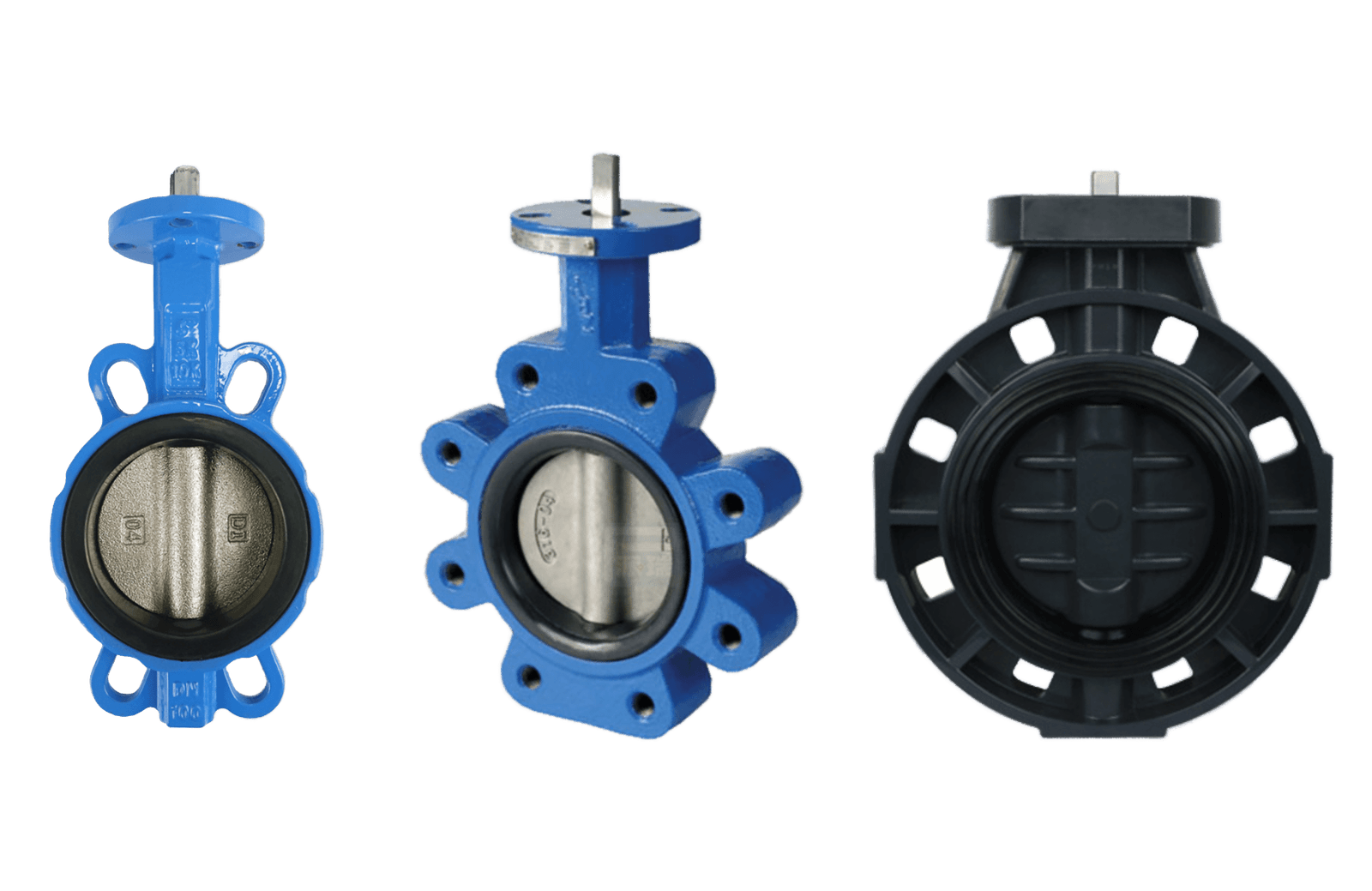
Butterfly Valve Bodies
Butterfly valves operate with a rotating disc that controls flow. They provide a compact and lightweight solution with quick operation.
- Advantages: Low cost and space-saving design.
- Disadvantages: Do not seal as tightly as ball valves and can create flow turbulence.
- Applications: Used in HVAC systems, water distribution, and slurry handling where space and weight are concerns.
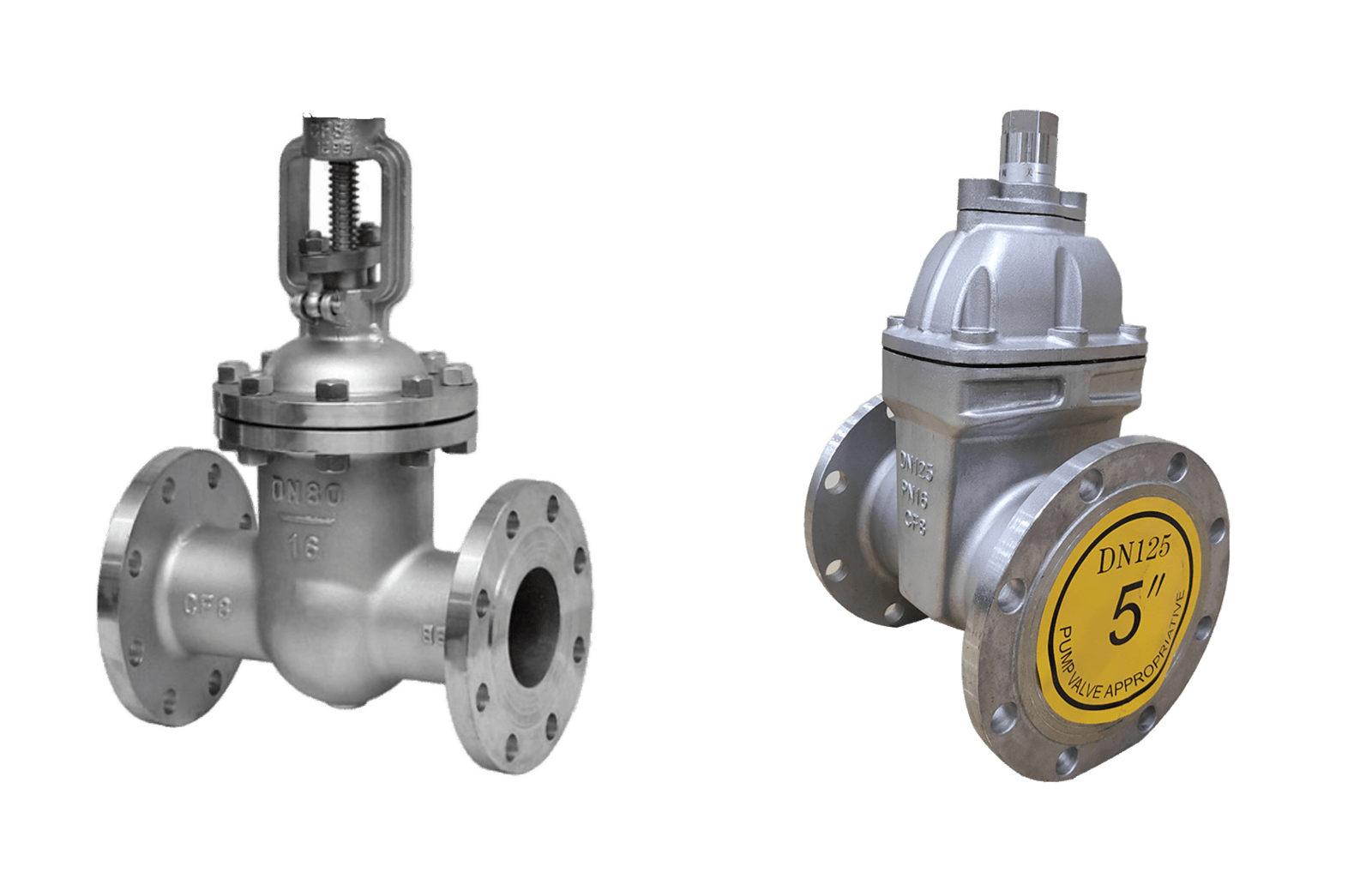
Gate Valve Bodies
Gate valves operate by lifting a gate out of the path of the fluid. This design provides minimal resistance to flow when fully open, making them ideal for on/off control.
- Advantages: Straight-through flow with low pressure drop.
- Disadvantages: Not suitable for throttling and can be slow to open and close.
- Applications: Used in water, oil, and gas pipelines where full flow is required.
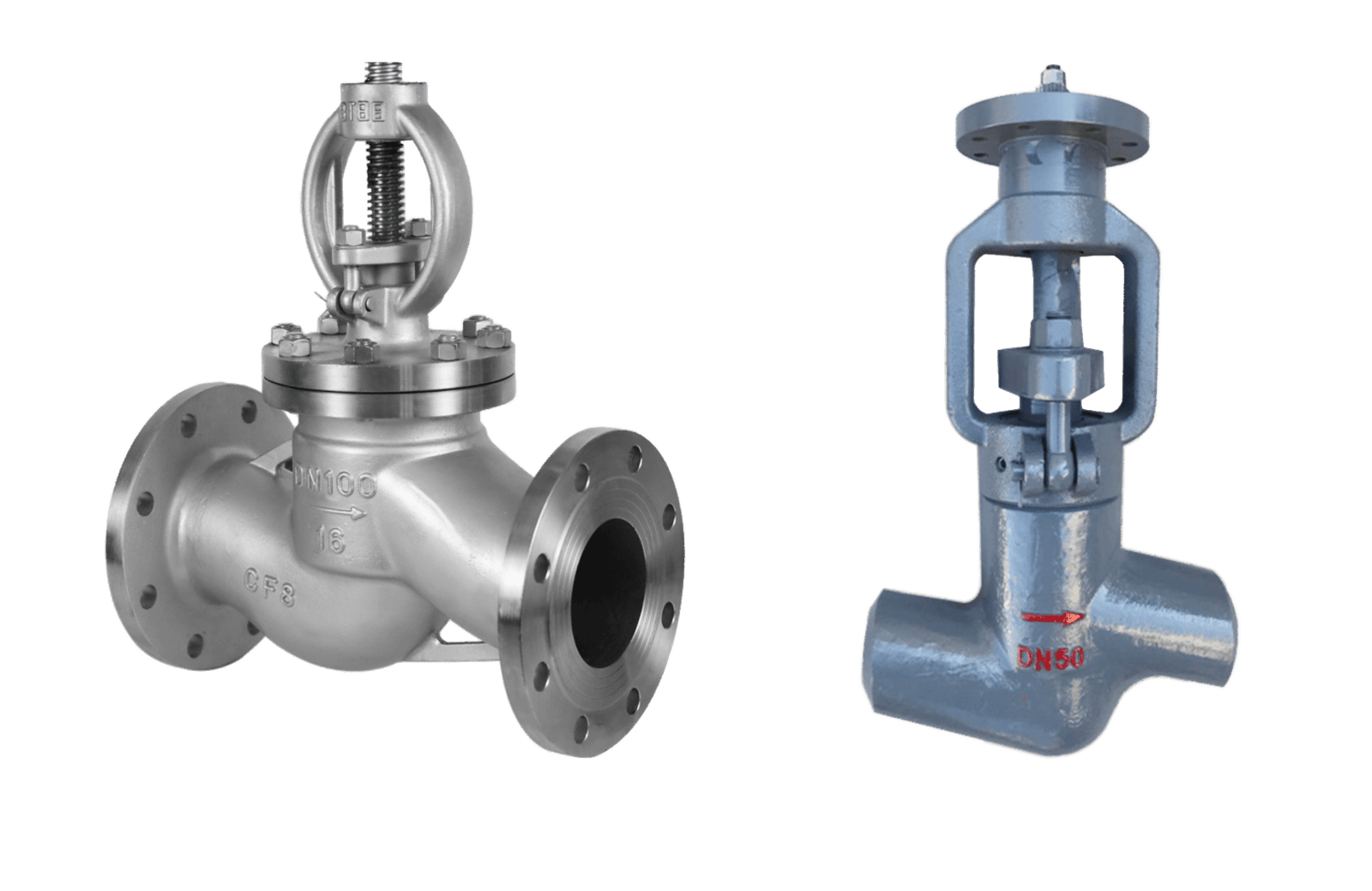
Globe Valve Bodies
Globe valves control flow by moving a disc perpendicularly to the flow stream. This allows for precise flow regulation.
- Advantages: Excellent throttling capabilities and good shutoff.
- Disadvantages: Higher pressure drop compared to gate valves.
- Applications: Ideal for water treatment, chemical processing, and steam systems where precise flow control is needed.
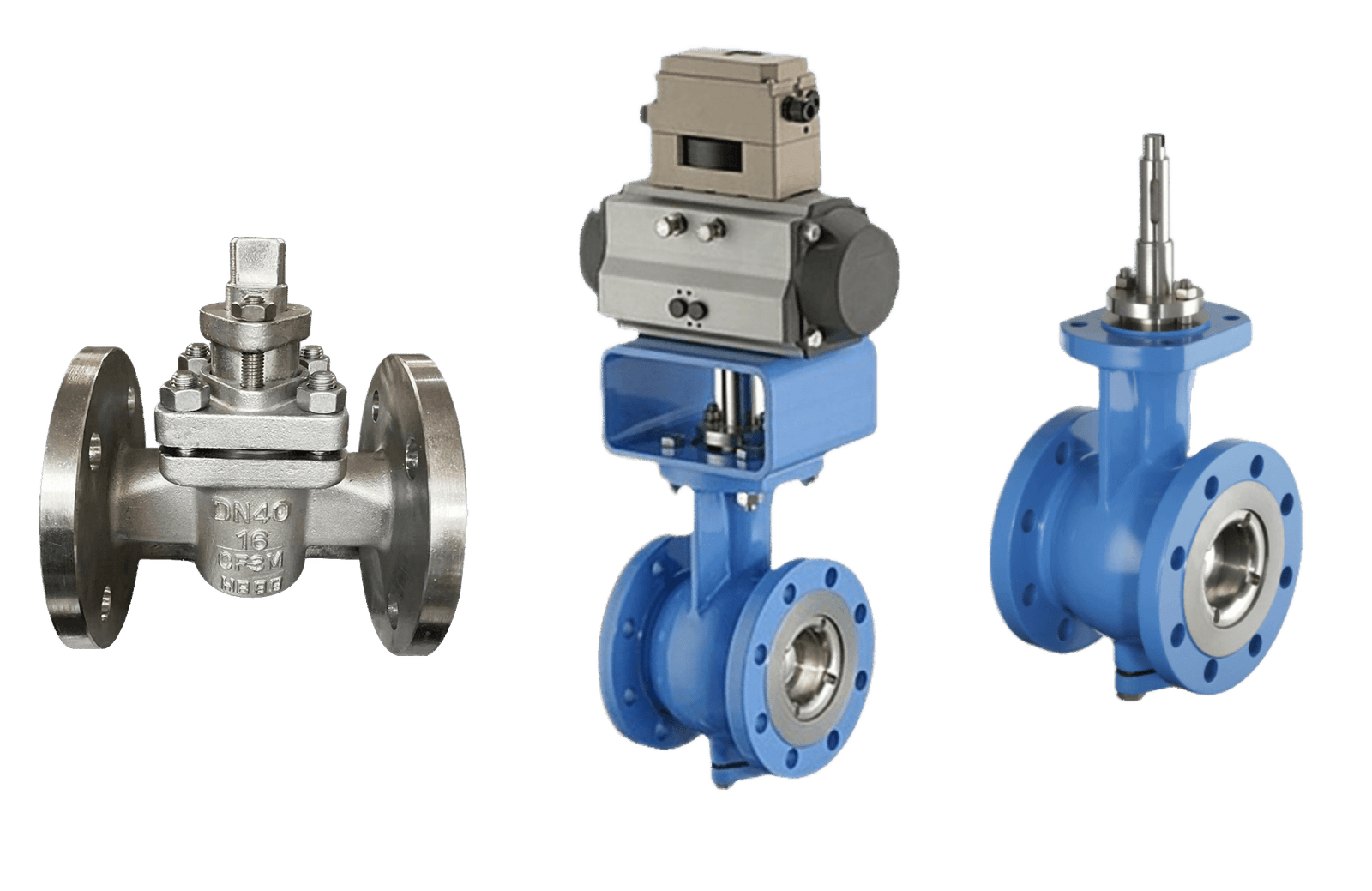
Plug Valve Bodies
Plug valves use a cylindrical or conical plug that rotates inside the valve body to control flow. They are robust and provide good shutoff.
- Advantages: Simple design and ease of maintenance.
- Disadvantages: Higher operating torque.
- Applications: Common in oil and gas, chemical, and water systems where a durable and easy-to-maintain valve is needed.
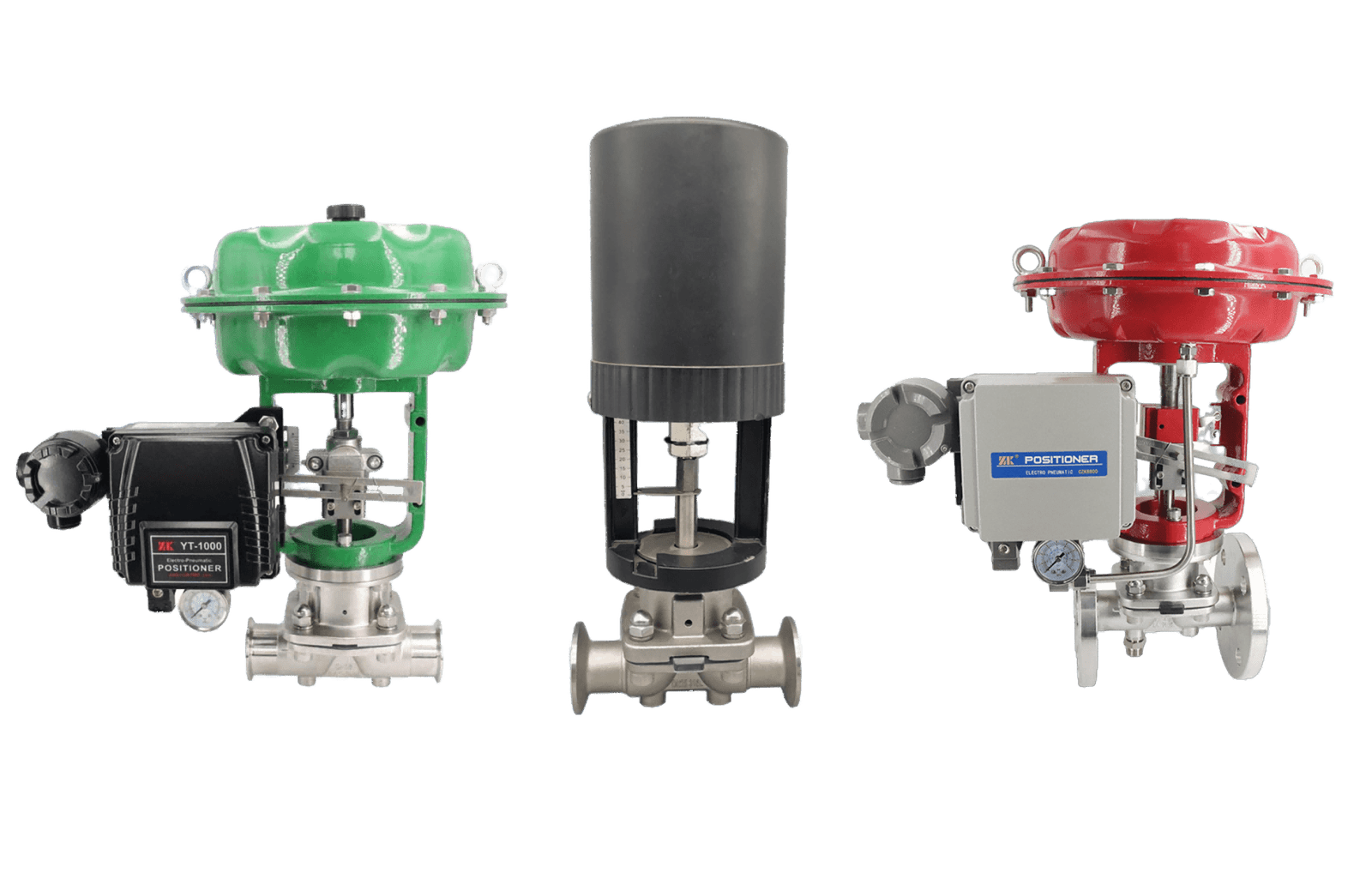
Diaphragm Valve Bodies
Diaphragm valves use a flexible diaphragm that presses against a seat to control flow. They are ideal for handling corrosive fluids and slurries.
- Advantages: Clean and tight shutoff.
- Disadvantages: Limited pressure and temperature ranges.
- Applications: Widely used in pharmaceutical, food and beverage, and chemical processing where contamination must be minimized.
Chapter 3: Control Valve Body Materials
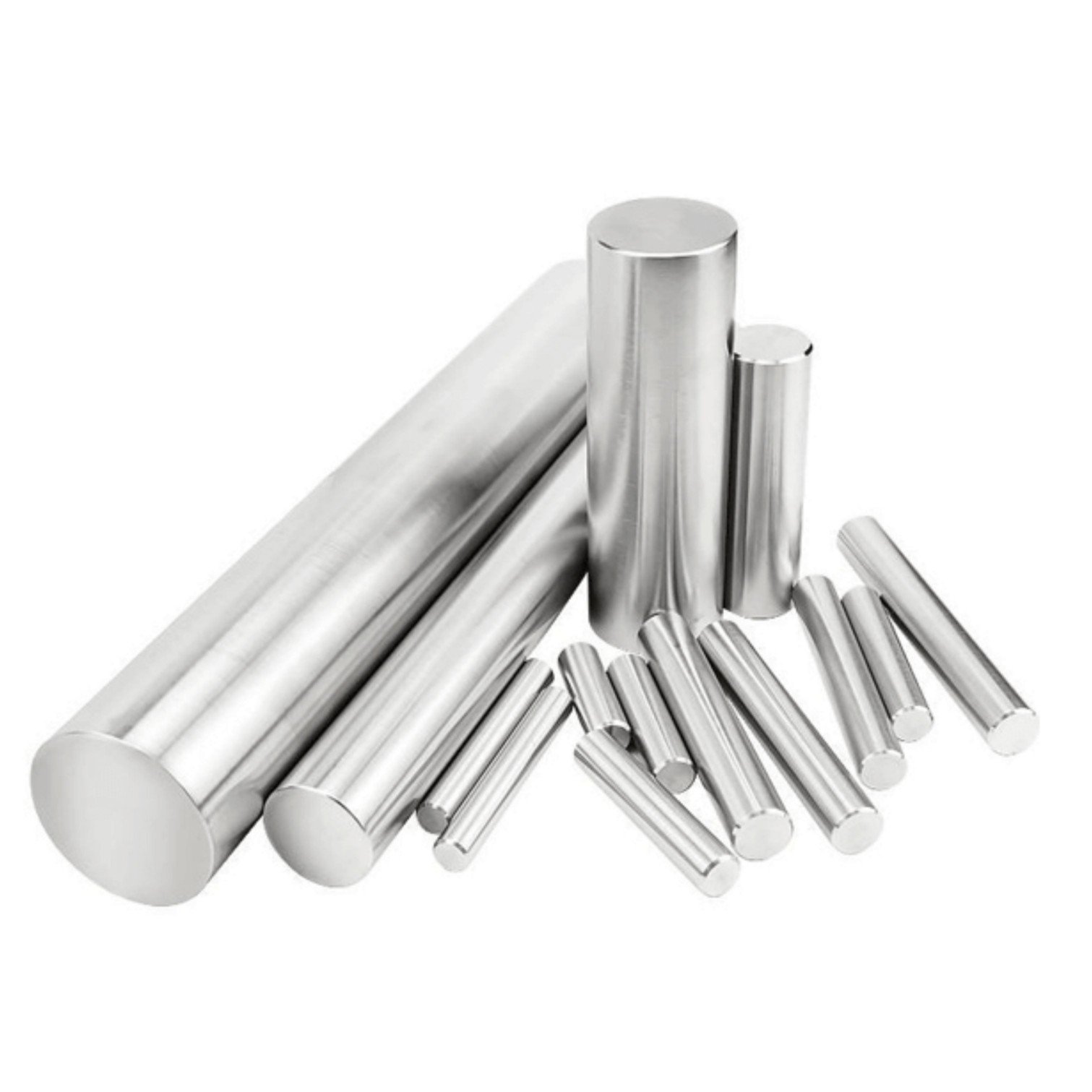
stainless steel
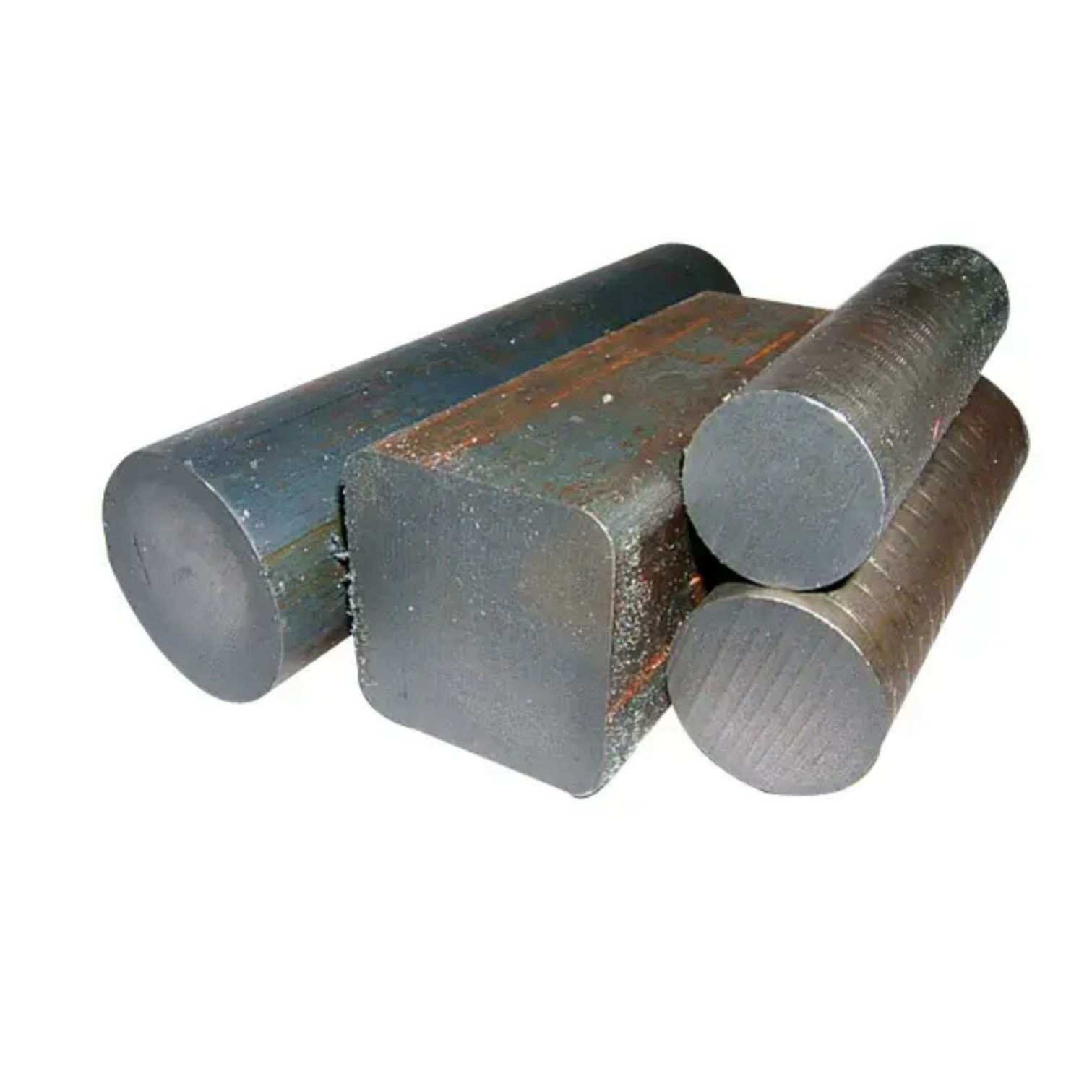
Cast iron
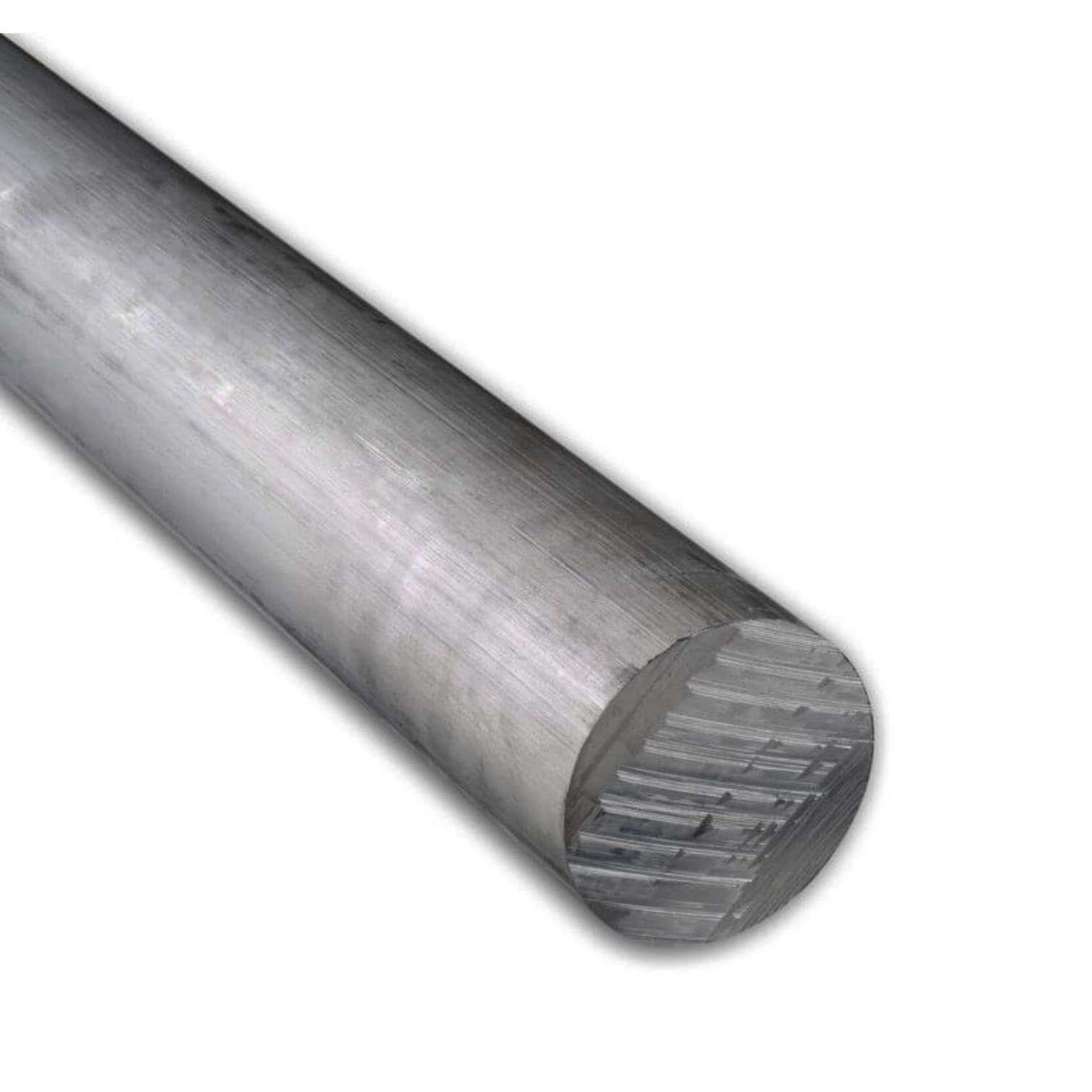
carbon steel
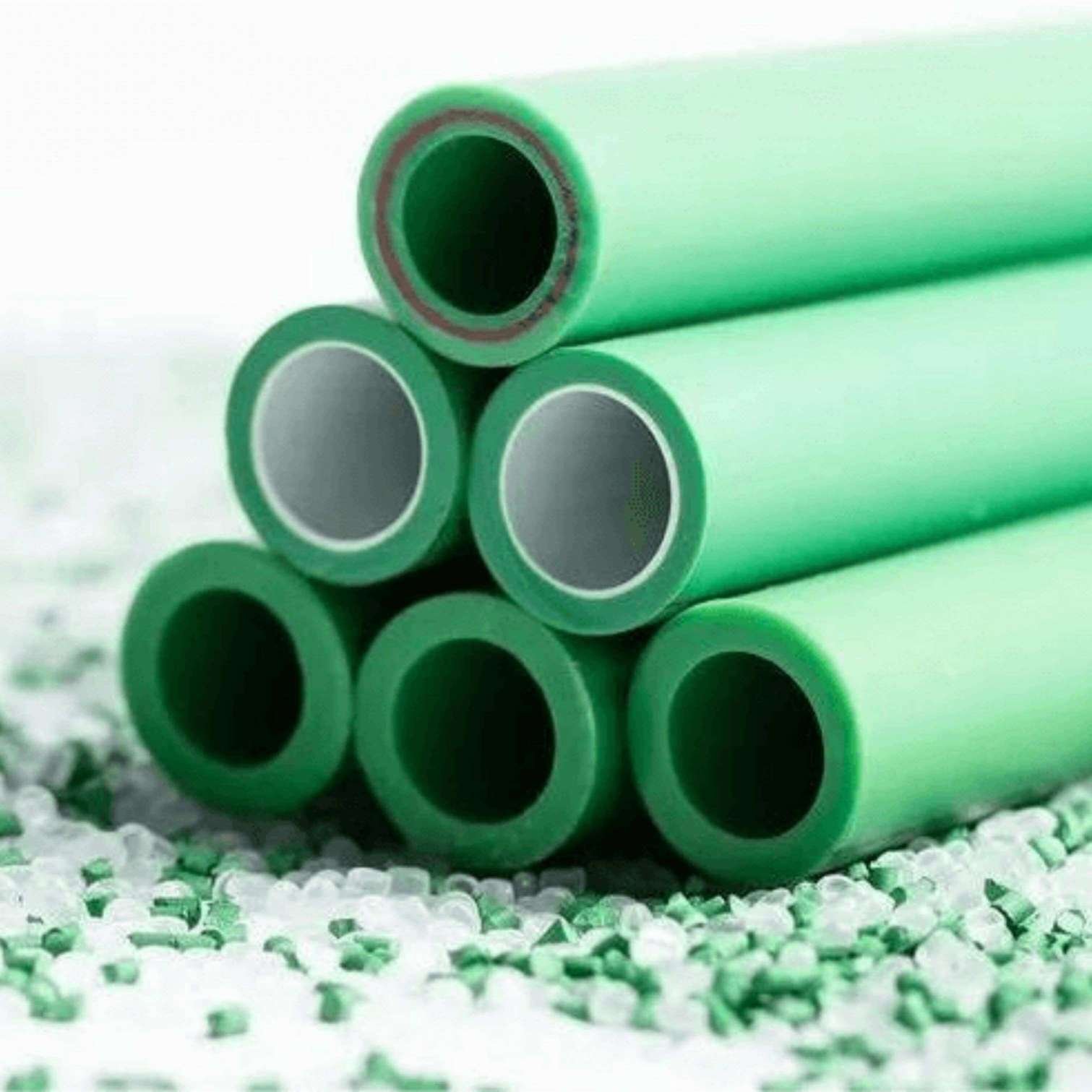
Plastic(PVC)
Dive into the world of control valve body materials, where the choice of alloys and composites plays a critical role in ensuring optimal performance and longevity in diverse operating conditions.
Stainless Steel: When it comes to durability and corrosion resistance, stainless steel steals the show. Variants like 304, 304L, 316, and 316L are like the reliable workhorses of the valve world, withstanding the harshest environments and corrosive fluids without breaking a sweat. From chemical plants to marine applications, stainless steel valves ensure peace of mind and long-lasting performance.
Cast Iron: Cast iron valves are known for their robustness and cost-effectiveness. While they may not offer the same level of corrosion resistance as stainless steel, they excel in applications where high-pressure and high-temperature conditions are prevalent. In my experience, cast iron valves are often used in HVAC systems, water distribution networks, and other applications where cost considerations and mechanical strength are priorities.
WCB (Carbon Steel): WCB, or carbon steel valves, are valued for their strength and versatility. These valves are suitable for a wide range of applications, from general industrial processes to high-pressure and high-temperature environments. In my experience, WCB valves are commonly found in power plants, refineries, and petrochemical facilities, where they offer reliable performance under demanding conditions.
Plastics: Plastic valves, such as PVC, uPVC, and CPVC, are lightweight and corrosion-resistant, making them ideal for certain applications. In my experience, these valves are commonly used in water treatment plants, irrigation systems, and chemical storage facilities. However, they may not be suitable for applications involving high temperatures or pressures, as they have lower temperature and pressure ratings compared to metal valves.
Comparing Practical Applications:In practical terms, stainless steel valves are preferred for their corrosion resistance and durability in harsh environments, while cast iron valves offer a cost-effective solution for high-pressure applications. WCB valves provide strength and versatility for various industrial settings, while plastic valves offer lightweight and corrosion-resistant options for specific applications. By considering the specific requirements of each application, engineers can select the most suitable material for control valve bodies, ensuring reliable performance and longevity in operation.
Other Materials: Additionally, control valve bodies can be constructed from a range of other materials, including brass, bronze, aluminum, and exotic alloys such as Hastelloy and Inconel, each offering unique advantages in specific applications.
Chapter 4: What is Sealing Mechanism in Valves
Effective sealing mechanisms are paramount in ensuring the integrity and reliability of industrial valves under diverse operating conditions.
Let’s delve into various sealing mechanisms utilized in valve engineering, drawing from two decades of experience in pipeline and valve engineering.
Gland Packing:
A time-tested sealing mechanism, involves wrapping packing material around the valve stem to create a compression seal upon gland tightening.
Pros:
- Suitable for high-temperature and high-pressure applications, offering robust sealing performance.
- Provides flexibility in accommodating shaft movements and irregularities in valve stems.
Cons:
- Requires periodic adjustments and maintenance, leading to potential downtime and operational disruptions.
- Prone to wear and friction-induced damage over time, necessitating regular replacement.
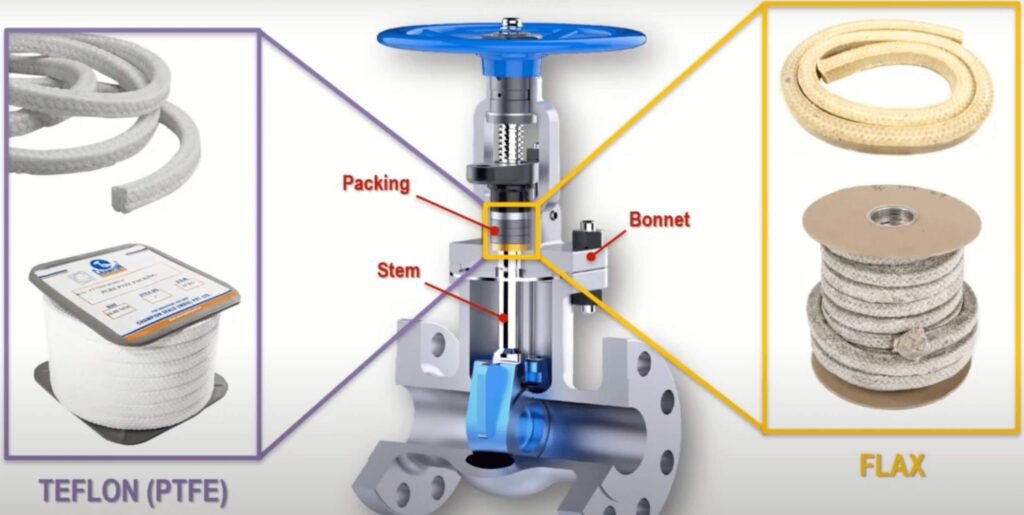
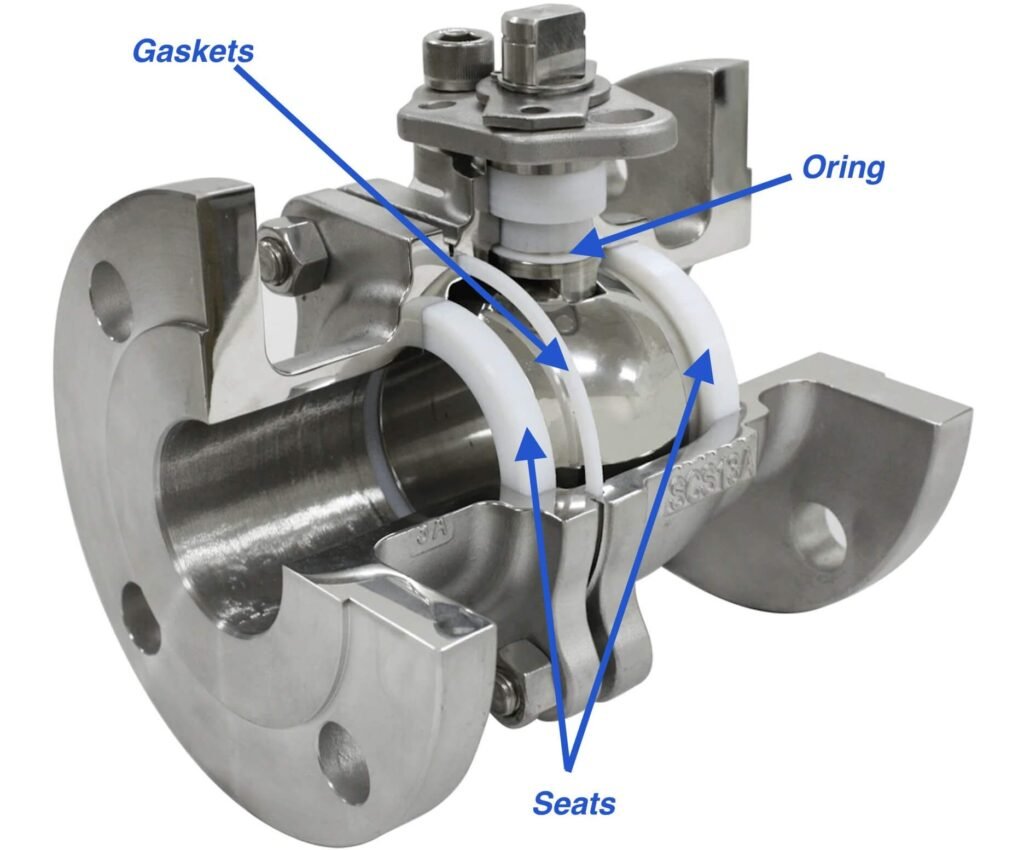
O-rings and Gaskets:
Elastomeric seals, including O-rings and gaskets, provide simple yet effective sealing solutions for a wide range of valve types.
Pros:
- Easy to install and replace, reducing downtime and maintenance costs.
- Cost-effective sealing solution suitable for various temperature and pressure ranges, ensuring versatility in application.
Cons:
- Limited to specific temperature and pressure ranges, requiring careful selection to avoid degradation and failure.
- May experience wear and deterioration over time, particularly in harsh operating environments, necessitating regular inspection and replacement.
Butterfly and Ball Valve Seats:
Sealing in butterfly and ball valves is achieved through elastomeric materials or metal-to-metal contact, offering effective sealing solutions for low to moderate-pressure applications.
Pros:
- Effective sealing performance for low to moderate-pressure applications, ensuring leak-free operation.
- Versatile sealing options available, including elastomeric seats and metal-to-metal contact, catering to diverse operational requirements.
Cons:
- May not be suitable for extreme temperature variations or aggressive chemical environments, limiting their application scope.
- Requires careful material selection and maintenance to prevent seat degradation and ensure long-term performance reliability.
Chapter 5: How many Sealing material in valve
Sealing Material | Temperature Range | Common Media | Characteristics | Disadvantages |
---|---|---|---|---|
Polytetrafluoroethylene (PTFE) | -200°C to 260°C (-328°F to 500°F) | Chemicals, acids, bases, solvents, gases | Excellent chemical stability and high temperature resistance. Suitable for various corrosive media and high temperature environments. | Limited resilience under high mechanical stress. May experience cold flow over time. Not suitable for applications with strong mechanical wear. |
Polyethylene (PE) | -50°C to 80°C (-58°F to 176°F) | Water, air, gases, some chemicals | Good chemical stability and wear resistance. Commonly used in general industrial applications for valve seals and packings. | Limited temperature resistance and may degrade under UV exposure. Not suitable for applications with high temperatures or exposure to harsh chemicals. |
Nitrile Butadiene Rubber (NBR) | -30°C to 120°C (-22°F to 248°F) | Petroleum products, oils, fuels, hydraulic fluids | Good oil resistance and abrasion resistance. Suitable for petroleum and lubricating oil media. Commonly used in valve seals and O-rings. | Limited resistance to ozone and oxygen. May degrade in the presence of strong acids or bases. Poor performance in applications with high temperatures. |
Fluoroelastomer (FKM/Viton) | -20°C to 200°C (-4°F to 392°F) | Fuels, oils, solvents, chemicals | Excellent oil resistance and high temperature resistance. Commonly used in high temperature and organic solvent media for valve seals and gaskets. | High cost compared to other sealing materials. May not be suitable for applications with exposure to steam or strong bases. Limited low-temperature performance. |
Silicone Rubber (VMQ) | -50°C to 230°C (-58°F to 446°F) | Water, steam, food products, pharmaceuticals | Good high temperature resistance and oxidation resistance. Suitable for high temperature steam and food media. Commonly used in valve seals and gaskets. | Poor resistance to abrasion and tearing. May degrade in the presence of certain chemicals or oils. Limited tensile strength compared to other elastomers. |
Ethylene Propylene Diene Monomer (EPDM) | -50°C to 150°C (-58°F to 302°F) | Water, steam, chemicals, acids, bases | Excellent weather resistance and aging resistance. Commonly used in outdoor applications and water systems for valve seals. | Limited resistance to petroleum-based fluids. May degrade over time when exposed to ozone or UV radiation. Performance may vary depending on the formulation. |
Graphite | -200°C to 600°C (-328°F to 1112°F) | High temperature gases, steam, corrosive chemicals | Excellent thermal conductivity and chemical resistance. Commonly used in high temperature and high pressure valve applications, such as in steam systems and refineries. | Limited resilience in applications with strong mechanical stress. May experience particle release, leading to contamination. Requires careful handling to prevent graphite dusting. |
Polypropylene (PP) | -10°C to 100°C (14°F to 212°F) | Water, chemicals, acids, bases | Good corrosion resistance and high temperature resistance. Commonly used in chemical and pharmaceutical industries for valve packings and gaskets. | Limited resistance to UV radiation and high temperatures. Not suitable for applications with exposure to strong oxidizing agents or hydrocarbons. |
Chapter 6: How many Valve end Connections: A Comprehensive Overview
What is Threaded Connections:
Have you ever noticed that valves often feature female threaded end connections designed to receive male threaded pipes? There are also variations, including valves with male threaded connections and those with one female and one male end. The key to a successful threaded connection lies in following standardized thread specifications, ensuring compatibility and proper sealing.
Common Thread Standards
In industrial settings, threaded connections must comply with established standards. Here are the commonly used threading standards in the valve industry:
NPT (National Pipe Thread): This is a widely used American standard for tapered threads, which ensures a fluid-tight seal without additional sealing materials. NPT threads are common in North American piping systems.
BSP (British Standard Pipe): Commonly used in Europe and other parts of the world, BSP threads come in two types: BSPT (tapered) and BSPP (parallel or straight). BSPT threads seal similarly to NPT threads, while BSPP threads require a soft seal like an o-ring.
G Threads: Also known as BSPP (British Standard Pipe Parallel), these are used for straight threads. G threads require a sealing washer or o-ring to ensure a leak-proof connection. They are common in many international applications.
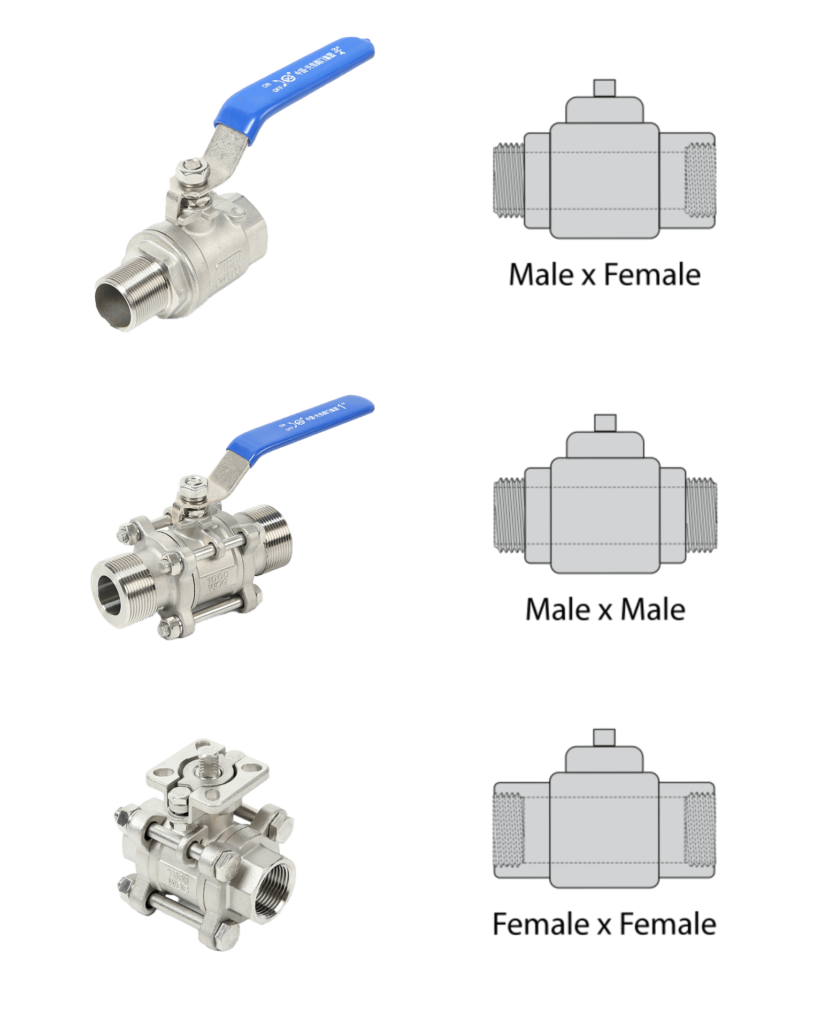
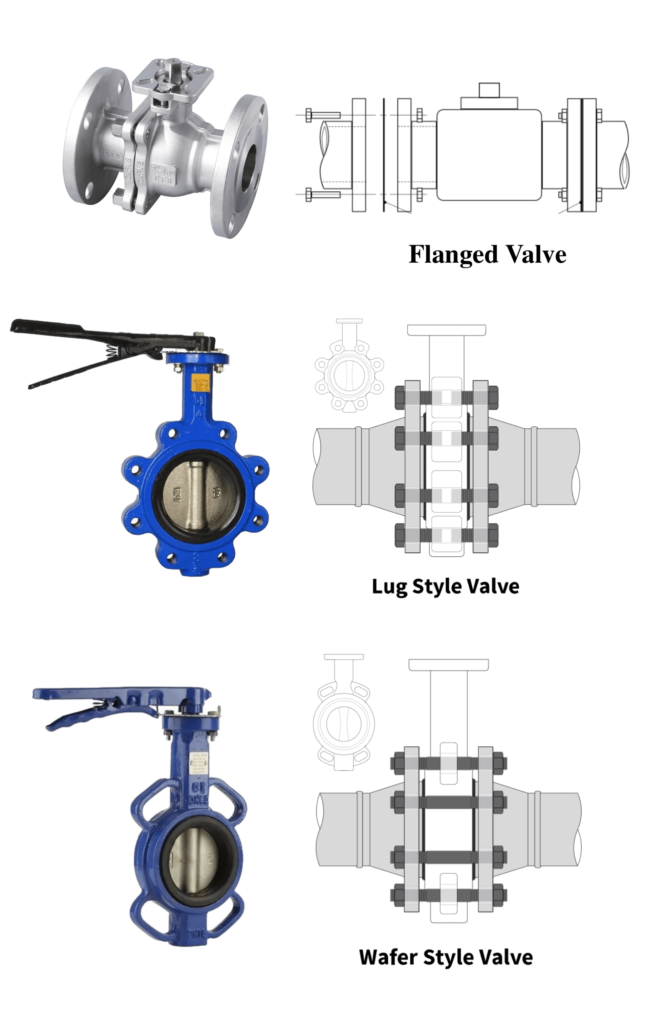
What is Flanged Connection:
Flange connections are among the most popular methods for attaching valves to pipelines. This method involves bolting two flanges together: one on the valve and the other on the pipeline, using bolts and nuts. Flange connections are favored for their ease of installation and maintenance, making them ideal for a wide range of applications.
Let’s explore the three main types of flange connections:
Normal Flange Style:
The traditional flange style involves welding the flanges directly onto the valve and pipeline ends. This method provides a robust and leak-proof connection, making it suitable for high-pressure and high-temperature applications. Its sturdy nature ensures reliability and durability, which are essential in demanding industrial environments.Wafer Style:
Wafer-style flange connections are designed to fit between two existing flanges without the need for additional bolts and nuts. This design is particularly useful in applications where space is limited or when a lighter valve design is preferred. The compact nature of wafer-style connections makes them an excellent choice for systems that require frequent handling and adjustments.Lugged Style:
Lugged-style flange connections feature lugs or ears on the valve body, allowing the valve to be bolted directly to the pipeline flanges. This type of connection offers significant flexibility during installation and removal, making it ideal for applications where frequent maintenance or valve replacement is expected. The lugs provide additional support and alignment, ensuring a secure fit.
Tri-Clamp Connection:
Tri-Clamp, also known as sanitary clamp connections, consist of three main components: two ferrules, a clamp, and a gasket. The ferrules are welded onto the ends of the pipes or valves. The clamp holds the ferrules together, with the gasket providing a secure and leak-proof seal between them. This design allows for quick assembly and disassembly, making maintenance and cleaning operations efficient and straightforward.
Tri-Clamp connections must adhere to specific industry standards to ensure compatibility and reliability. Here are the three primary standards for sanitary Tri-Clamp fittings:
DIN (Deutsches Institut für Normung): This German standard is known for its precision and is widely used in European industries. DIN standards ensure high quality and reliable performance in sanitary applications.
ISO (International Organization for Standardization): ISO standards are recognized globally and provide guidelines for dimensions, tolerances, and materials, ensuring that Tri-Clamp fittings are compatible across different regions and applications.
BS (British Standard): The British Standard for Tri-Clamp fittings is commonly used in the UK and other regions. BS standards ensure that fittings meet stringent quality and safety requirements.
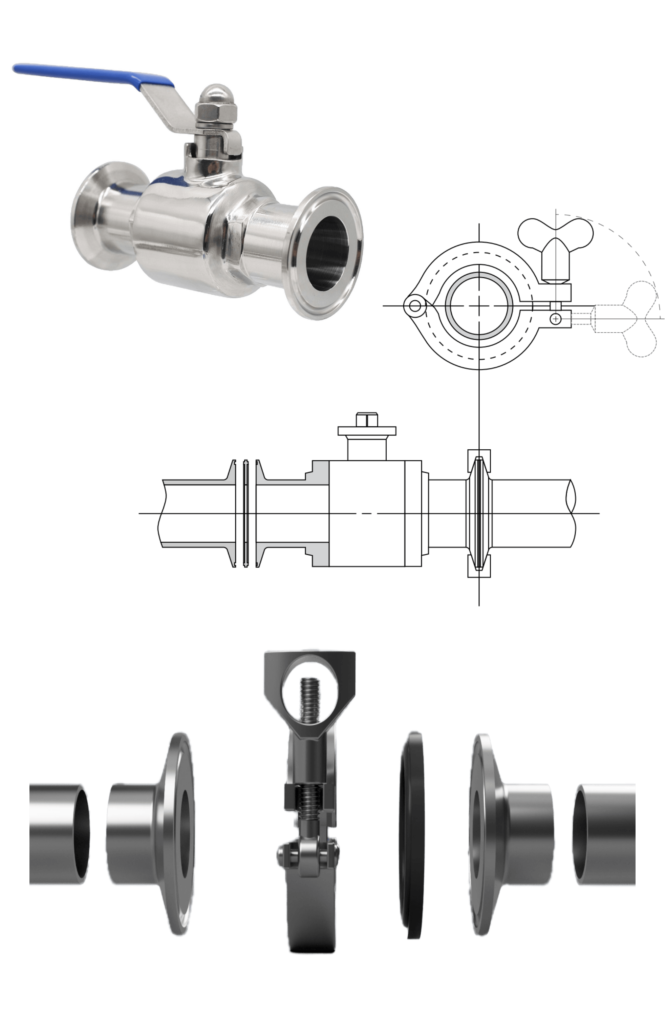
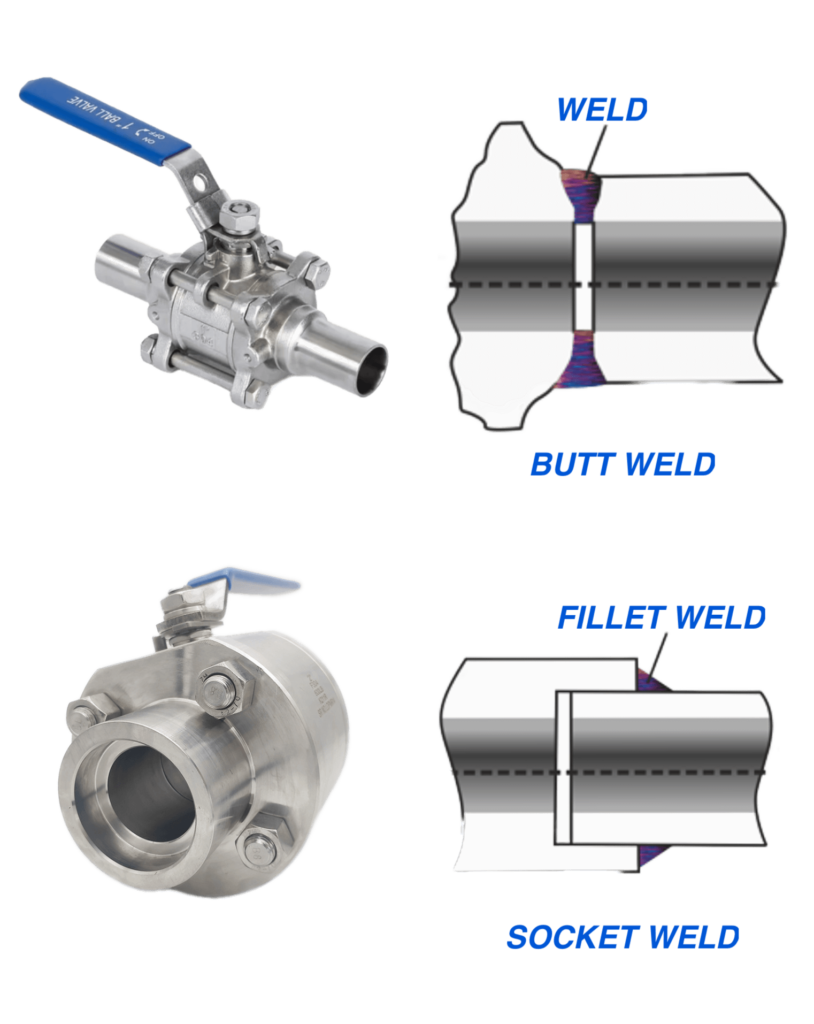
Welded Connection
Welded connections involve permanently joining the valve to the pipeline through various welding methods. These connections offer robustness and leak resistance, making them suitable for demanding applications. The main welded connection methods include:
Butt Weld: Butt weld connections involve welding the end of the valve directly to the pipe end, creating a smooth and seamless joint. This type of connection is commonly used in large-sized valves and critical applications where leak-tightness and structural integrity are paramount.
Socket Weld: Socket weld connections involve inserting the pipe into a recessed area (socket) on the valve and then welding around the joint. This type of connection provides a strong and reliable joint, particularly suitable for small-sized valves and high-pressure applications. Socket weld connections offer improved flow characteristics compared to threaded connections.
Other Welding Methods: Additional welding methods such as fillet welds or groove welds may also be used depending on the valve and pipeline materials, as well as the application requirements.
Connection for pvc Pipe system
Union Connection: Union connections involve two threaded ends that can be easily connected or disconnected using union nuts. This type of connection allows for quick installation and removal of valves for maintenance or replacement without requiring tools. Union connections are commonly used in applications where frequent disassembly is required, such as in plumbing systems or portable equipment.
Glue Socket Connection: Glue socket connections involve using adhesive to bond the valve to the pipe. This type of connection offers quick and easy installation in PVC, UPVC, and CPVC piping systems. Proper surface preparation and adhesive selection are crucial to ensure a strong and durable joint.
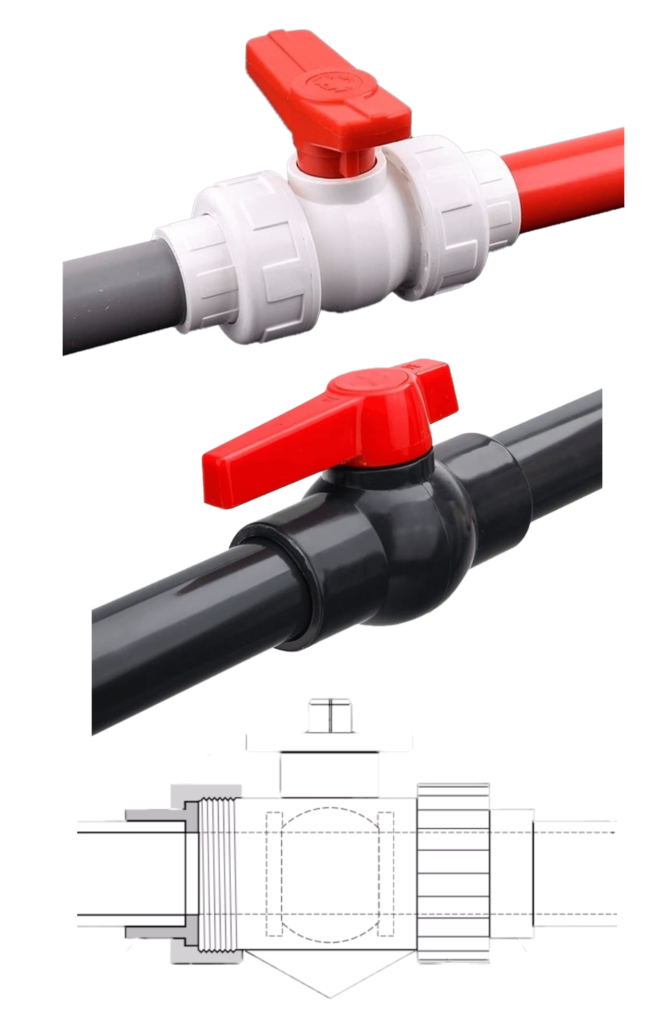